Chassis evolution: Harmonizing form and function
For a project this big, you need a solid foundation to begin with. This foundation was created with our improved chassis. Our goals for the chassis included the expansion in the front for more space for the electrical components, a flexible way to position and fixate them and compatibility with the drivetrain/suspension system of Meyer-1.
To meet those requirements and some more, it was clear to make a custom-built assembly that combines the structural main frame and the electronics box. A difficult part of this lightweight assembly was, to seal it enough to protect the electrical components against rain and other particles.
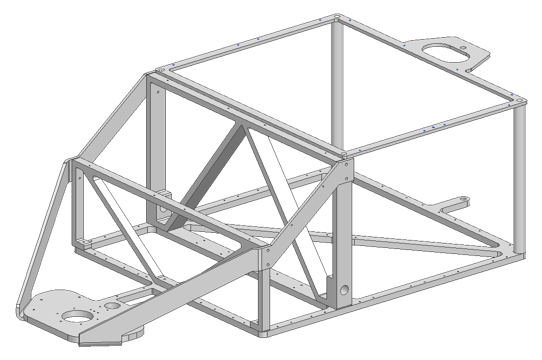
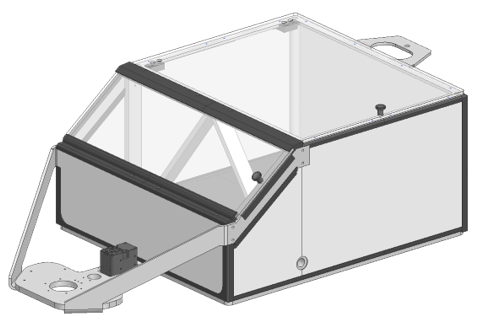
The first version of the chassis had an aluminum base frame that can bear the entire load of the rover. To make sure this is the case, multiple FEM-simulation (Finite element method) of the frame were made. The chassis must withstand loads from the rover weight and further stress while completing tasks like picking up a rock with the robotic arm.
The base frame was encased with a layer of polystyrene plates. Instead of a fixed mounting, the plates had a slide system with custom 3D-printed slot mountings on top and bottom. The plates at the bottom were printed as well. This enables the individual positioning of the electronic components with thread inserts in the plates. A huge advantage with this approach is the possibility to adapt fast to changes in the layout or addition of components.

With the further development of Thommen and the changes all around and within the chassis the sliding system didn’t work out as intended. Too many parts obstructed the plates from sliding out. Another downside of the first version was that the plugs in the thin polystyrene plates flexed too much.
With the development of the deep drill assembly the chassis needed to be sturdier than before. Therefore, many improvements were combined to a second iteration of the chassis.
The most obvious change would be the replacement of the white side plates with carbon fiber ones. With the new plates, not only are they durable enough for the plugs but they give additional strength to the structure. Some parts of the aluminum frame were improved as well to better stabilize the structure in the regions with the highest loads.
During the upgrade for the chassis, multiple new components were implemented. One of those were bigger fans for the cooling system. With the new arrangement of two big fans on the underside as intake and four smaller fans blowing out the warm air at the top, a minor overpressure is created within the chassis. The advantage with this is that no dirt particles will enter the chassis through the small gaps.
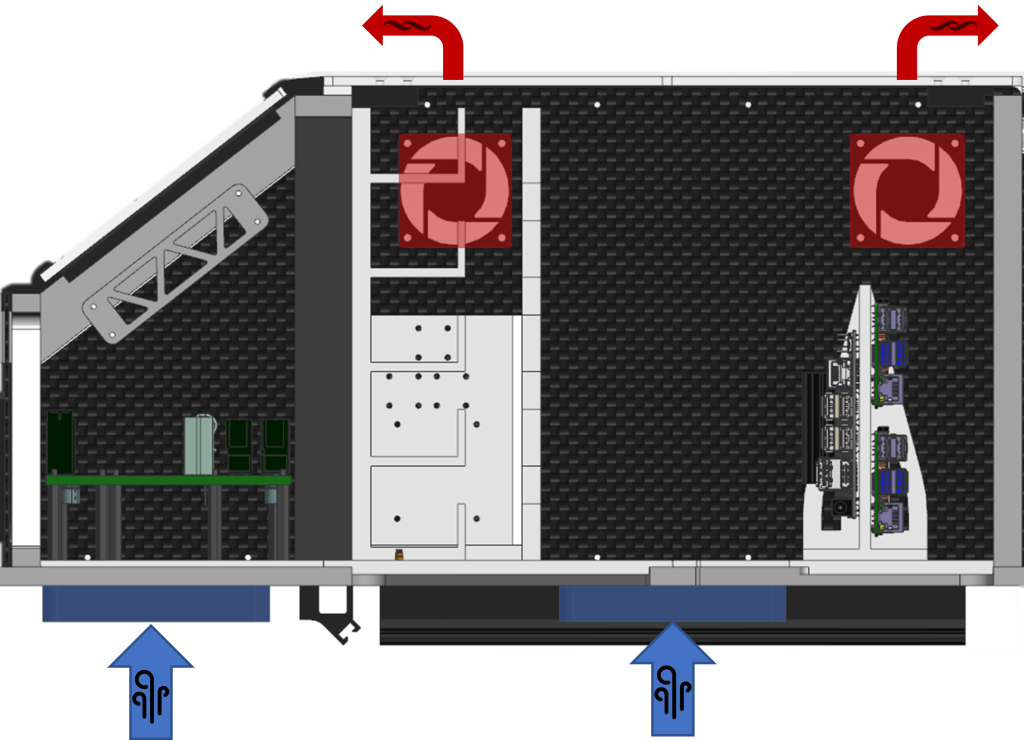
The newest version convinces with a modern look that meets all our requirements thanks to the iterative design approach. The increased volume and flexible system on the inside represent a huge improvement to its predecessor. The chassis is a great example of continuous engineering endeavor to achieve the best results.
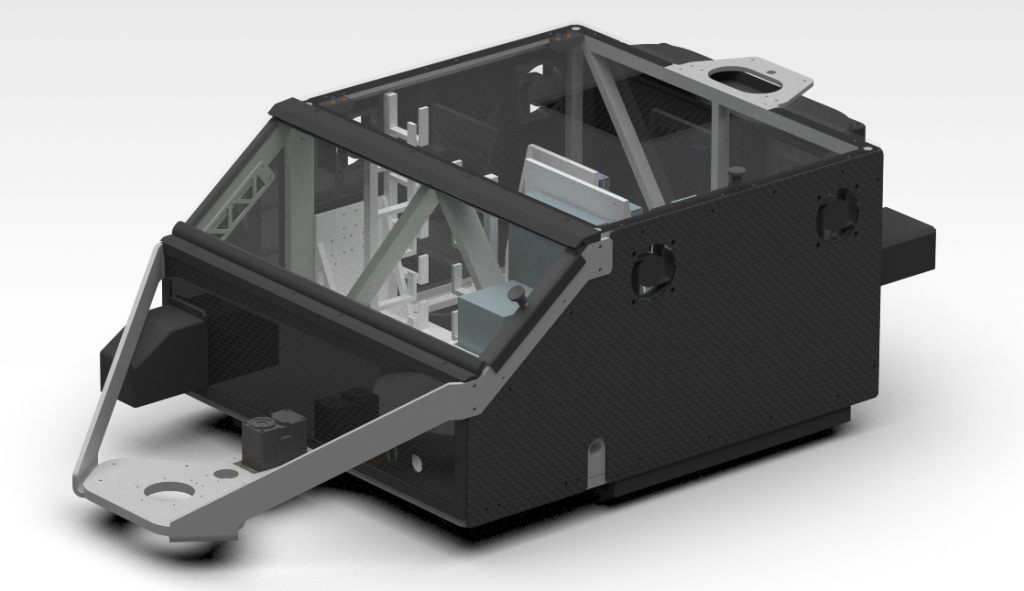
Comments
No comment posted about Chassis evolution: Harmonizing form and function