Chassis V3.0
Looking ahead to the ERC24, the FHNW Rover Team has planned many innovations and revisions, which also place new demands on the rover’s chassis. Some of these requirements include more space inside the chassis, a new mounting point for the upcoming drivetrain and the integration of a system that allows for the batteries to be hot-swapped.
As the central component of the rover, the chassis must withstand numerous forces. In order to make the chassis to be as light as possible, it is important to plan the absorption of these forces well. Wherever possible, an attempt was made to achieve 2D state of stress, i.e. no forces act vertically on the walls. As a result, the side walls can absorb a large proportion of all forces despite being so thin. To withstand the moment generated by the drivetrain, a U-profile runs right through the chassis. This reinforces the overall structure and can also be used as a mounting point for the Deepdrill. To check whether the chassis could withstand the forces, several FEM simulations were carried out in addition to manual calculations.
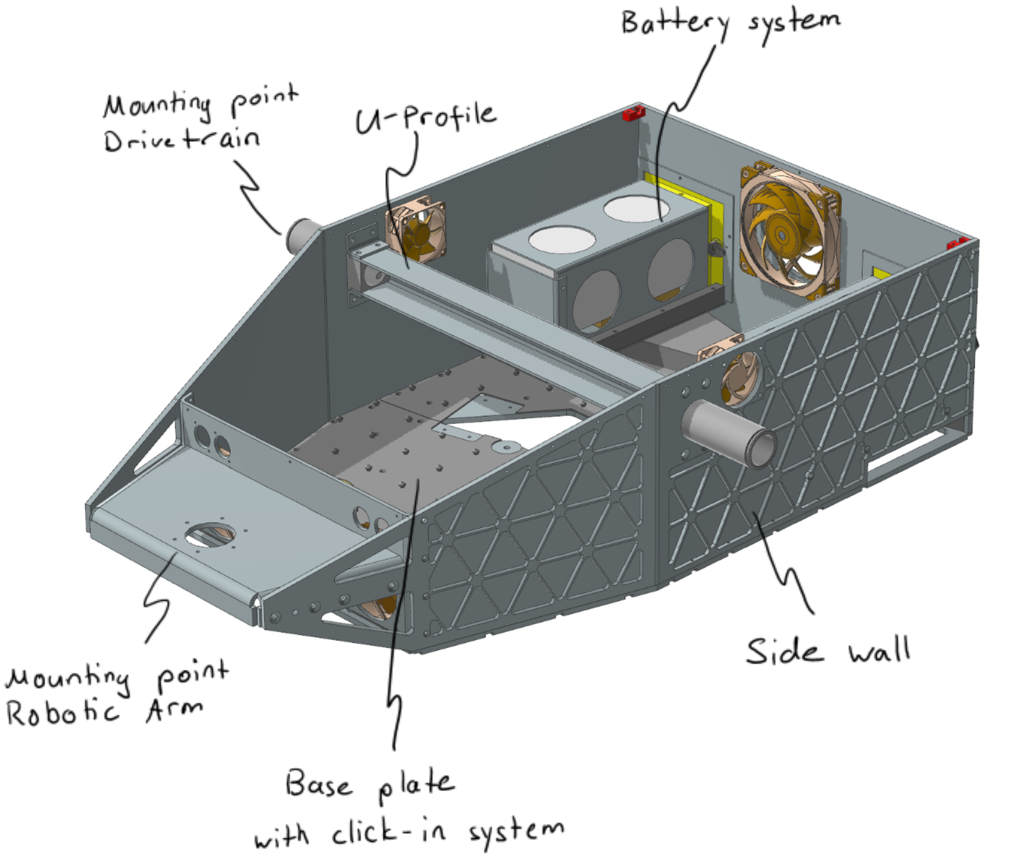
The biggest challenge in developing the concept was to find a good fit between all the components mounted to the chassis. The weight distribution of the entire rover also had to be assessed. The chassis should be as balanced as possible so that the rover is not front or rear-heavy.
The side and rear panel were technically challenging to manufacture. The outer contour of the parts was jet cut from a 6mm thick aluminum plate. A large part was further milled to a wall thickness of only 1.5mm. To make this possible, an Isogrid structure was required. The final step was to bend both side walls.
The use of bent parts was quite a challenge. As many bent parts come together in the front part of the Cassis, each with a certain tolerance, some degrees of freedom had to be left in the design.
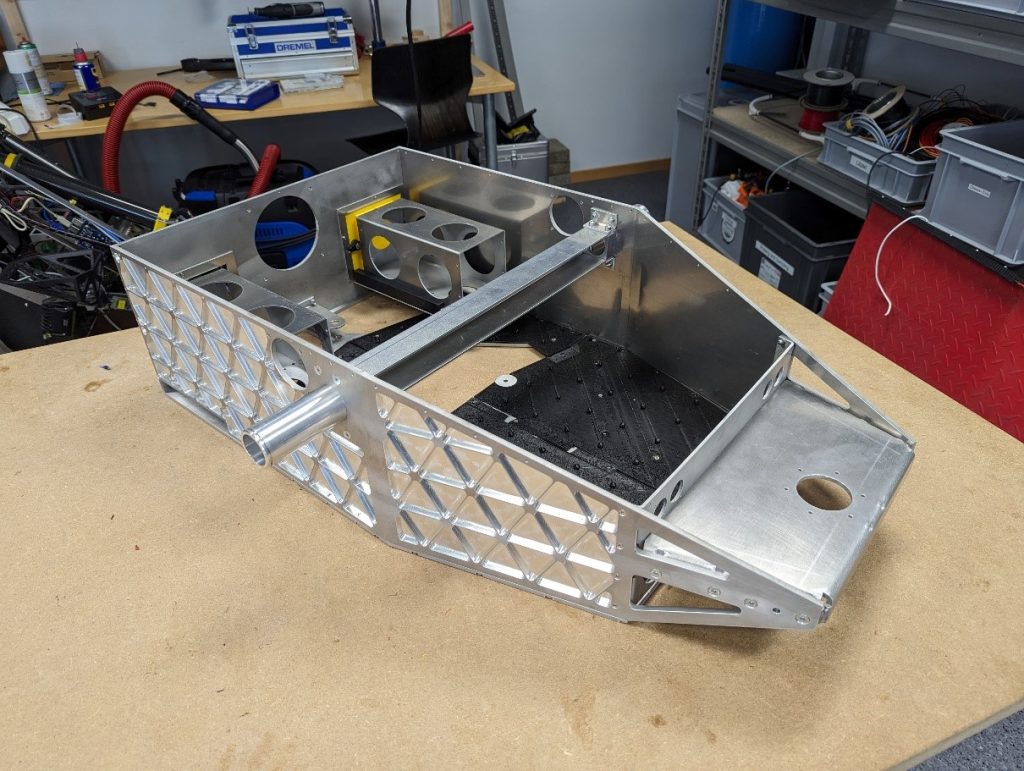
The chassis features a new system for changing the batteries with two advantages. The batteries can be changed without having to switch off the rover as well as the possibility to operate the rover with two batteries, resulting in a longer operational time. The batteries can be inserted like drawers at the rear of the rover, no further plugging in is needed. This makes it easy and convenient to change and makes it possible to configure the batteries according to energy requirements.
A base plate with a snap-in system was developed to enable modular placement of electronic components and cable guiding within the chassis. The system allows for a quick installation and removal as well as great flexibility.
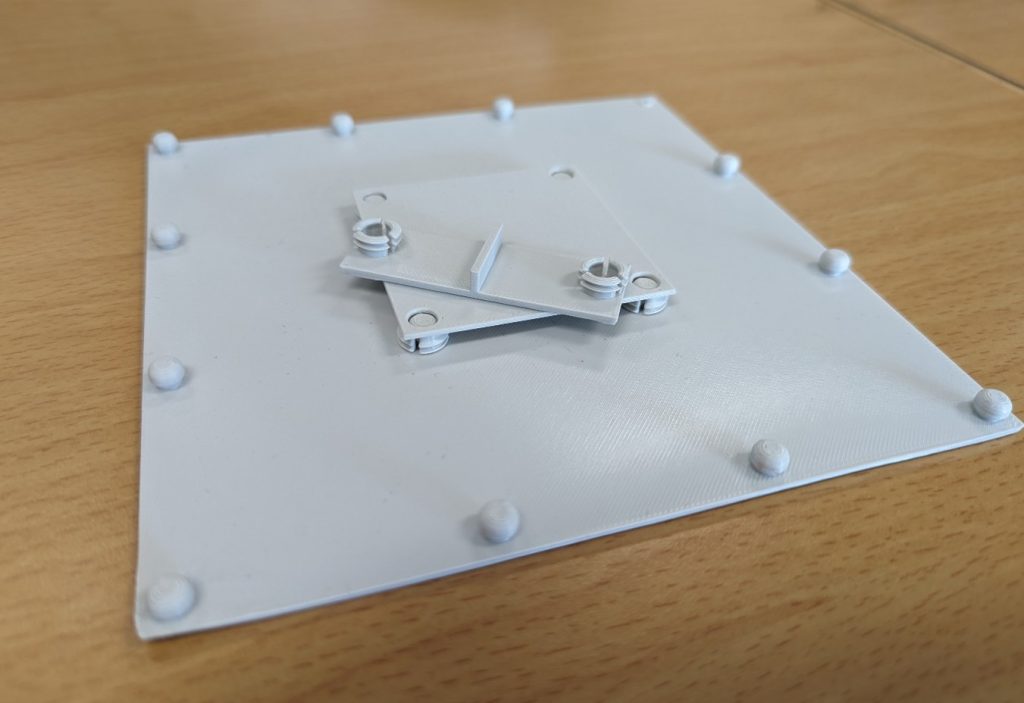
The Rover team is looking forward to seeing the assembly of all components in action on the upcoming testing days!
Comments
No comment posted about Chassis V3.0