I’ve got the POWER!
Based on the experience gained on the ERC23, the FHNW Rover Team has planned various revisions. The most significant change is to double the system supply voltage from the unregulated battery voltage around 24V to 48V. This allows us to have a more powerful drivetrain. To achieve a longer operating time for the rover, we added a second battery and a hot-swappable system for it.
Concept
The power supply is an essential component of the Rover. Therefore, it must function reliably and under continuous load. A lot of effort went into the consideration of the system, and we came up with the solution described below.
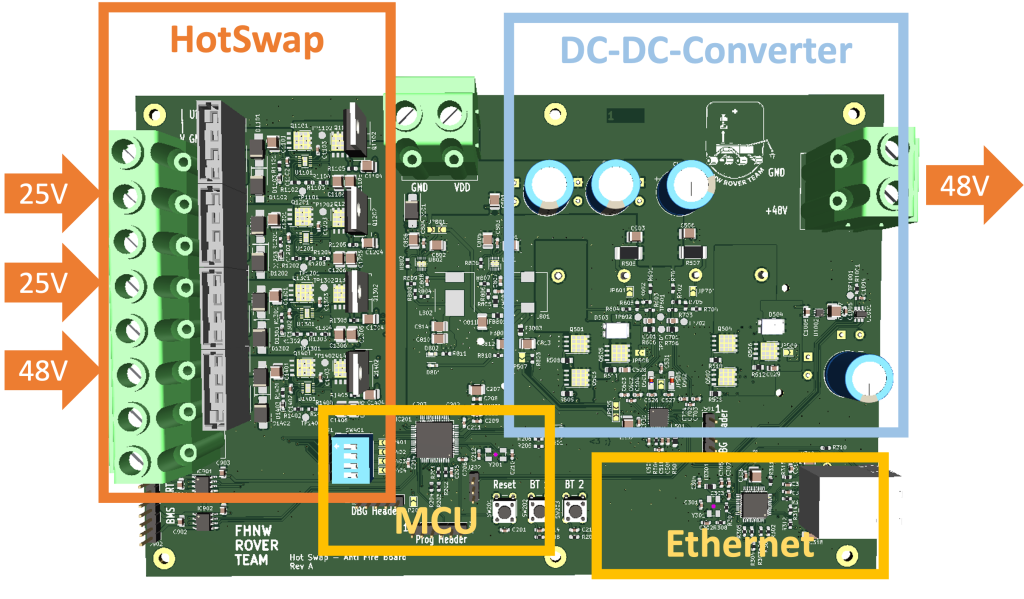
DC/DC
Since the batteries have output voltage between 21V and 30V and the new rover operates at 48V, we had to design a step-up converter. The design challenge was to support the peak-power consumption we measured at the ERC23, plus some extra puffer. So, we decided to look for a converter with 500W peak-power. We couldn’t find a converter that would meet all our needs and since it is very interesting to design such a device, we built it ourselves.
Most of the effects we had to learn on the hard way. For example, lots of the power MosFETs ended up in smoke. Overall, we toked away a lot from revision A. The next step now is to finish rev B, so that the new system gets powered completely from our solution.
Hot-Swap
The aim was to avoid having to shut down the entire system just to connect a new battery. We also wanted to increase the capacity at the same time. The solution was, to place two batteries in the system. These are then controlled via different channels. Each channel is set up with by using an Ideal Diode Controller (LM7481). These consist of two back-to-back N-Fets. Through this, a microcontroller can switch a channel on or off. The system protects itself to not short the batteries together. A seamless transition between multiple sources is now possible.
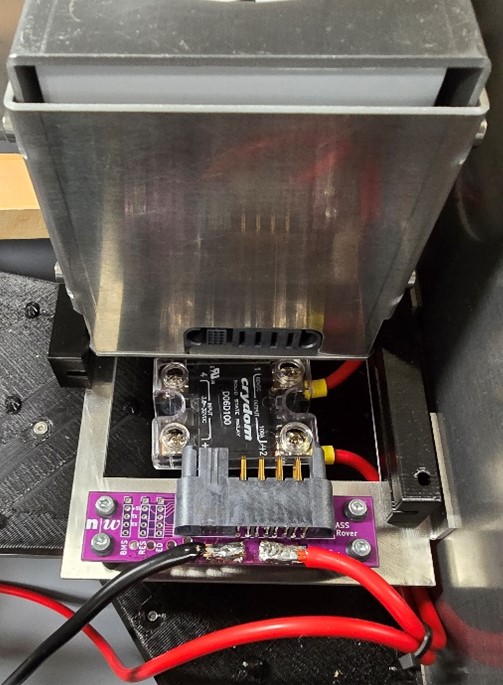
Complete system
Thanks to our sponsor SwayTronic we got an 22Ah super powerful Li-Po battery, which we placed with a BMS on a drawer. To connect the battery in the Rover, a powerful and robust connector is used, which has data pins for the connection to the BMS. This allows us to easily change the settings of our BMS and receive data like voltage, current and state of charge. The battery and the BMS are set up in a drawer, so a fast and easy change is possible.
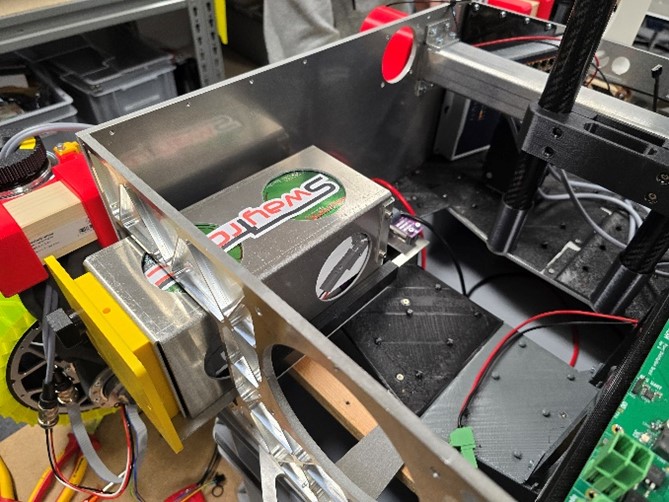
The requirements of the ERC call for an emergency stop, which de-energizes the system completely. We solved this with individual solid-state relays after each battery. However, we have also installed an emergency halt to only stop the moving parts and prevent so the shutdown of the whole system.
We are currently installing the various components in the chassis and wiring the electronic components. The FHNW Rover Team is looking forward to the first drive of our new Rover Hufi!
Comments
No comment posted about I’ve got the POWER!